Non-destructive testing (NDT) is a vital process used across many industries to evaluate the integrity and reliability of components and materials without causing any damage. This form of testing plays a crucial role in ensuring the safety and efficiency of various products, structures, and systems. Exploring the benefits of non-destructive testing (NDT) allows us to understand the importance of this technique in identifying flaws, defects, and inconsistencies, ultimately preventing potential failures and accidents. In this article, we will delve into the advantages of NDT third party inspection services and its significant impact on enhancing quality control and safety in different sectors.
Non-destructive testing (NDT) is a set of techniques used in science and industry to evaluate the properties of a material, component, or system without causing damage. This allows for inspection and testing without affecting the future use of the object being tested. NDT is commonly used in manufacturing, construction, and in-service inspections to ensure product integrity and reliability, to control manufacturing processes, lower production costs, and to maintain a uniform quality third party quality inspection level. The benefits of NDT include cost savings, improved safety, and increased productivity, among others. These methods are crucial in ensuring the safety and reliability of critical infrastructure such as bridges, pipelines, and aircraft, as well as in the manufacturing of essential products across various industries. NDT offers a non-invasive, accurate, and efficient means of testing materials and components, contributing to overall quality assurance and cost-effectiveness.
Non-destructive testing (NDT) encompasses a range of methods such as ultrasonic testing, radiography, third party inspection companies in egypt eddy current testing, magnetic particle testing, and visual inspection, among others. These techniques allow for the examination of materials and components without causing damage, making them essential in industries where product integrity and safety are paramount. This approach not only saves time and money by avoiding the need for destructive testing but also facilitates the early detection of defects, ensuring that potential issues are identified and addressed before they lead to costly failures. NDT methods are widely used in sectors like aerospace, automotive, energy, construction, and manufacturing, where the quality and reliability of materials and components are vital. By leveraging NDT, organizations can optimize their operations, enhance safety, and ultimately deliver better products and services.
The Importance of Non-Destructive Testing (NDT) in Industry

Non-destructive testing (NDT) is crucial in various industries to ensure the safety, reliability, and efficiency of structures, products, and materials. By using NDT techniques such as ultrasonic testing, radiography, eddy current testing, and magnetic particle inspection, flaws and defects can be detected without causing damage to the tested materials. NDT plays a vital role in industries such as aerospace, automotive, construction, manufacturing, and energy. It helps in identifying defects such as cracks, corrosion, and weld integrity issues, thereby preventing potential failures that could lead to costly downtime, accidents, and environmental hazards. Moreover, NDT enables companies to comply with regulatory standards and requirements, allowing them to produce and maintain high-quality products and infrastructure. It also helps in extending the lifespan of assets and reducing maintenance costs by identifying issues at an early stage. Overall, the implementation of NDT in various industries is essential for ensuring operational safety, minimizing risks, and maintaining the overall integrity and performance of assets.
Common Methods Used in Non-Destructive Testing (NDT)
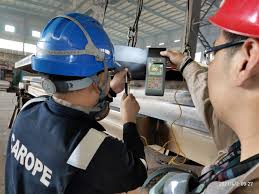
Some common methods used in non-destructive testing (NDT) include: 1. Visual inspection: This involves the use of eyes or cameras to inspect a material or component for any visible defects or abnormalities. 2. Ultrasonic testing (UT): UT uses high-frequency sound waves to detect internal flaws or measure the thickness of a material. 3. Radiographic testing (RT): RT uses X-rays or gamma rays to examine the internal structure of a material for defects or discontinuities. 4. Magnetic particle testing (MT): MT is used to detect surface and near-surface flaws in ferromagnetic materials by magnetizing the material and applying iron particles to reveal any defects. 5. Liquid penetrant testing (PT): PT involves applying a liquid dye or fluorescent material to a material's surface, which penetrates into surface-breaking defects to make them visible under specific lighting conditions. 6. Eddy current testing (ET): ET is used to detect surface and near-surface defects in conductive materials by inducing an electrical current in the material and measuring the electromagnetic field around it. These methods are widely used in various industries, including aerospace, manufacturing, construction, and automotive, to ensure the integrity and safety of materials and components without causing damage to them.
Advancements in Non-Destructive Testing (NDT) Technology
third party inspection services
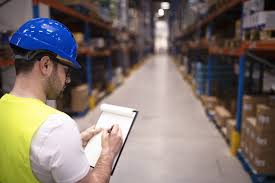
Non-destructive testing (NDT) technology has seen significant advancements in recent years, making it possible to detect and evaluate flaws in materials without causing any damage. Some of the key advancements in NDT technology include the use of digital radiography, which allows for faster and more accurate inspection of welds and other materials. Additionally, advancements in ultrasonic testing have improved the portability and accuracy of this method, allowing for more comprehensive inspections in a variety of industrial settings. Other innovations in NDT technology include the development of advanced imaging techniques, such as computed tomography, and the integration of artificial intelligence for automated defect recognition. These advancements have improved the efficiency and reliability of NDT inspections, making it an essential tool for ensuring the safety and quality of various industrial processes and products.
The Role of Non-Destructive Testing (NDT) in Quality Control
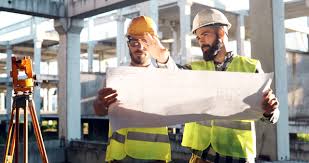
Non-destructive testing (NDT) plays a crucial role in quality control by allowing for the evaluation and inspection of materials, components, and structures without causing damage. This helps to ensure the safety, reliability, and integrity of products and assets in various industries, such as manufacturing, construction, aerospace, and automotive. NDT methods, such as ultrasonic testing, radiographic testing, magnetic particle testing, and dye penetrant testing, enable the detection of defects, discontinuities, and abnormalities that may compromise the quality and performance of a material or component. By using NDT, manufacturers and inspectors can identify potential issues early in the production process, leading to cost savings and improved product quality. In addition to identifying defects, NDT also allows for the monitoring of material properties and dimensions, verification of weld quality, and assessment of structural integrity. This information is essential for ensuring compliance with industry standards and regulations, as well as for meeting customer requirements. Overall, the role of NDT in quality control is to provide accurate and reliable data that enables informed decision-making and helps prevent catastrophic failures, ultimately contributing to the overall safety and success of products and structures.
Benefits of Non-Destructive Testing (NDT) for Structural Inspections
Non-destructive testing (NDT) for structural inspections offers several benefits, including cost-effectiveness, minimal disruption to operations, and the ability to identify issues without damaging the structure. NDT methods such as ultrasonic testing, radiography, and magnetic particle inspection can provide accurate and reliable results, allowing for proactive maintenance and preventing costly structural failures. Additionally, NDT can be used to assess the integrity of materials and components without the need for disassembly or removal, saving time and resources while ensuring the safety and longevity of structures.
Non-Destructive Testing (NDT) for Welding and Fabrication
Non-Destructive Testing (NDT) for welding and fabrication is a method used to evaluate the quality of a weld or fabricated component without causing any damage to the object being tested. This is important in ensuring the structural integrity and safety of the finished product. Common NDT methods for welding and fabrication include visual inspection, ultrasonic testing, radiography, magnetic particle testing, and dye penetrant testing. These methods can detect defects such as cracks, porosity, and incomplete fusion in welded joints, as well as other imperfections in fabricated components. NDT is essential in maintaining the quality and reliability of welded and fabricated structures in industries such as construction, manufacturing, and aerospace.
The Future of Non-Destructive Testing (NDT) in Aerospace
The future of Non-Destructive Testing (NDT) in aerospace is expected to continue to evolve with advanced technologies and techniques. As the aerospace industry progresses, the demand for more reliable and efficient NDT methods to ensure the safety and integrity of aircraft components will only increase. One area of growth in the future of NDT in aerospace is the use of automated and robotic inspection systems. These systems can provide faster and more accurate inspections, reducing human error and increasing overall productivity. Additionally, the use of advanced imaging technologies such as digital radiography and computed tomography will continue to play a significant role in NDT for aerospace, allowing for detailed and comprehensive inspections of complex aerospace components. Furthermore, the integration of artificial intelligence and machine learning into NDT processes will enable the development of predictive maintenance and continuous monitoring systems. This will help to identify potential issues before they become critical, leading to improved safety and reliability of aircraft. Overall, the future of NDT in aerospace is likely to be driven by advancements in automation, digital imaging, and data analysis. These developments will not only enhance the efficiency of NDT inspections but also contribute to the continued safety and reliability of aerospace systems.
Training and Certification for Non-Destructive Testing (NDT) Professionals
Training and certification for Non-Destructive Testing (NDT) professionals typically involves a combination of classroom instruction, hands-on practical training, and examinations to demonstrate proficiency in various NDT techniques such as ultrasonic testing, radiography, eddy current testing, and magnetic particle testing. There are several organizations that offer NDT training and certification, such as the American Society for Nondestructive Testing (ASNT) and the British Institute of Non-Destructive Testing (BINDT). These organizations have established guidelines and standards for NDT training programs and certification exams to ensure that NDT professionals have the necessary knowledge and skills to perform their jobs effectively and safely. NDT professionals can pursue different levels of certification, such as Level I, Level II, and Level III, depending on their qualifications and experience. These levels typically require a combination of classroom training, work experience, and passing a written and practical examination. Continuing education and renewal of certification is often required to maintain NDT certification, as technology and industry standards evolve. This may involve completing additional training courses, attending conferences and workshops, and demonstrating ongoing proficiency in NDT techniques. Overall, training and certification for NDT professionals are essential for ensuring that NDT personnel have the skills and knowledge needed to perform their jobs effectively and safely in various industries, including aerospace, oil and gas, manufacturing, and construction.